Nelson: iMac Pro VESA mount gets screwed
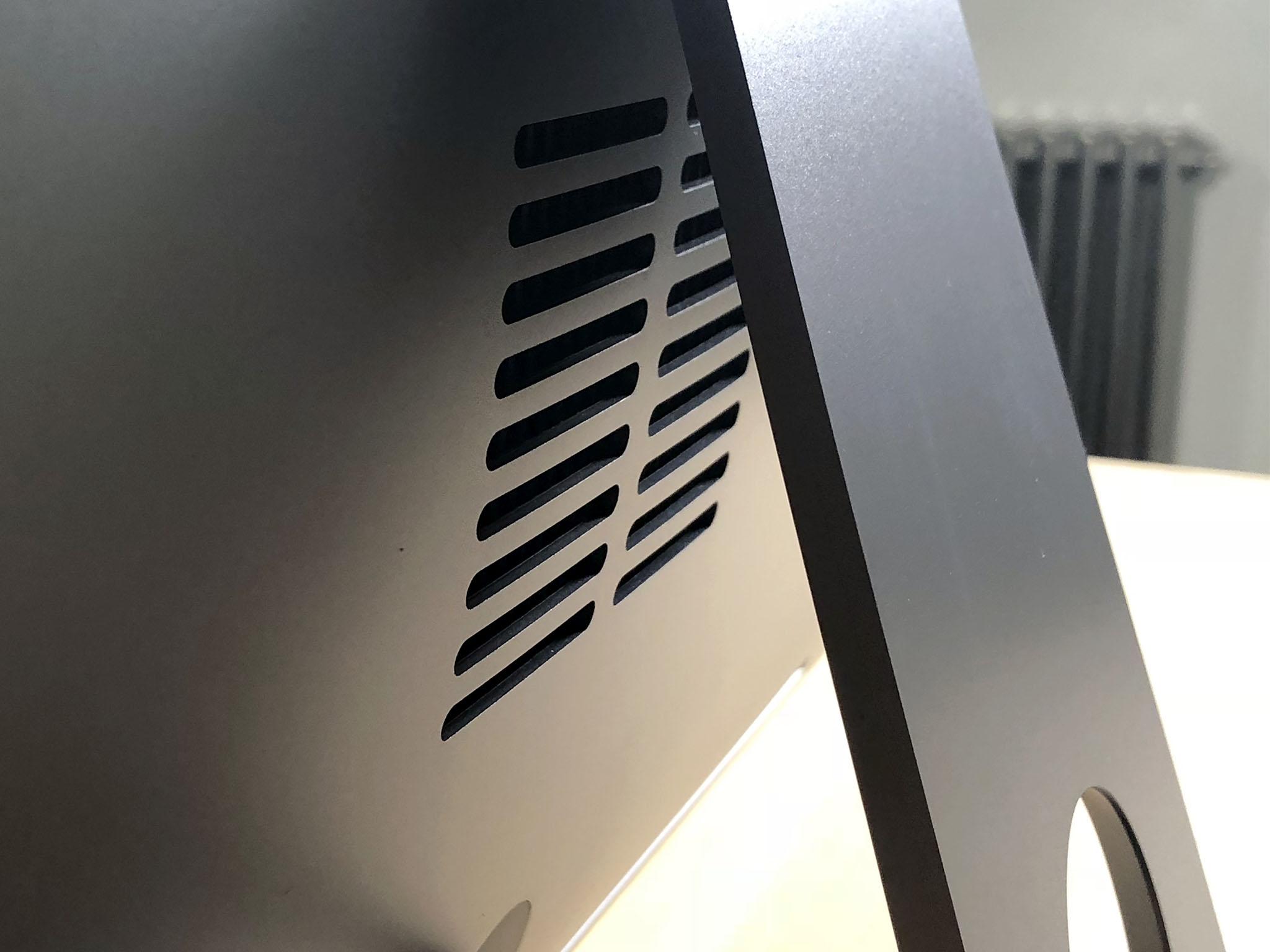
Quinn Nelson bought a VESA mount kit for his iMac Pro. Put it on, went to take it off, and a screw broke. He went to put it on again and another screw broke. After not getting anything approaching functional support from AppleCare, he took it to an Apple Store and, after waiting much longer than expected, he got scratched, mangled parts back for his trouble.
Nelson appears to have done everything right and remained cool — even gracious — throughout his ordeal. I don't know how the store let him leave with the parts in that condition. If it'd been me, I'd still be camped out at that Apple Store until everything was perfect. Including better quality screws.
And yes, this is getting attention because popular on YouTube. There are many people who have problems every day that don't get the same attention, because not popular on YouTube.
But this isn't about directing attention to solve any one person's bad support experience. It's about using attention to raise the bar for everyone.
Hopefully, this helps with that.
iMore offers spot-on advice and guidance from our team of experts, with decades of Apple device experience to lean on. Learn more with iMore!
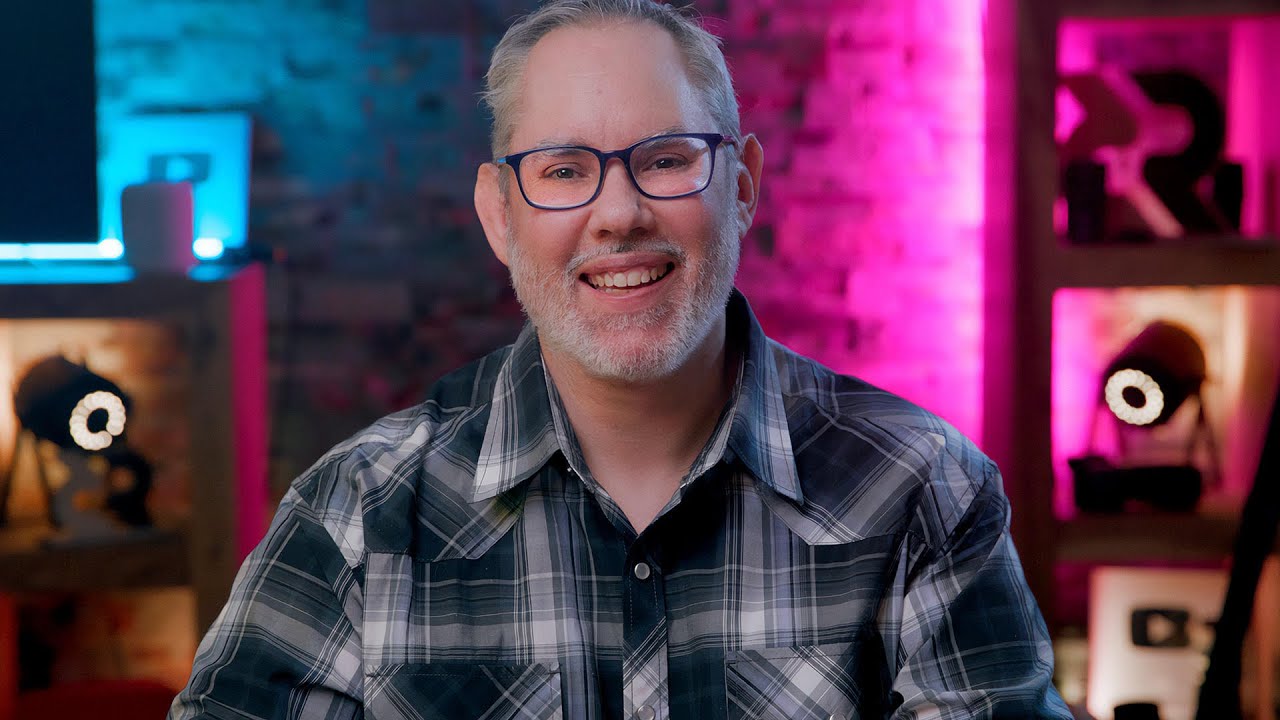
Rene Ritchie is one of the most respected Apple analysts in the business, reaching a combined audience of over 40 million readers a month. His YouTube channel, Vector, has over 90 thousand subscribers and 14 million views and his podcasts, including Debug, have been downloaded over 20 million times. He also regularly co-hosts MacBreak Weekly for the TWiT network and co-hosted CES Live! and Talk Mobile. Based in Montreal, Rene is a former director of product marketing, web developer, and graphic designer. He's authored several books and appeared on numerous television and radio segments to discuss Apple and the technology industry. When not working, he likes to cook, grapple, and spend time with his friends and family.