Apple has discovered that humans are better at assembling products than robots
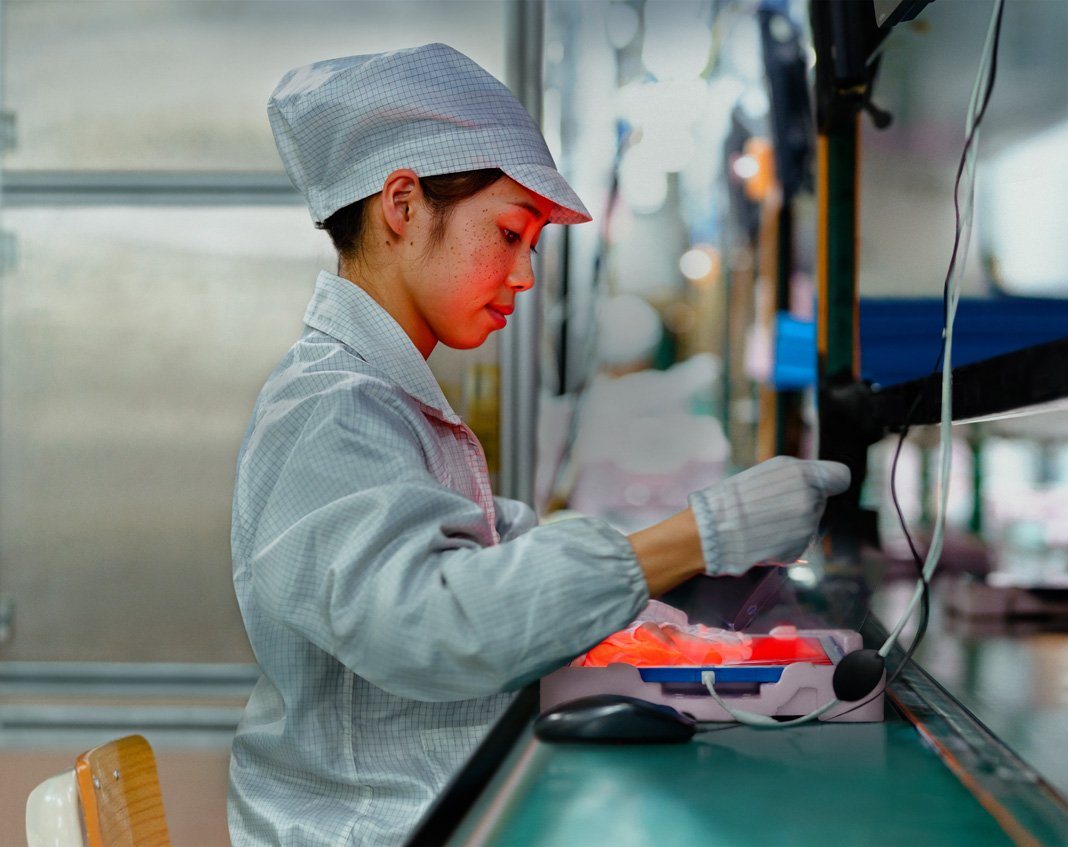
What you need to know
- Apple has reportedly been testing automated iPhone assembly.
- It worked with manufacturing partner Foxconn to develop an experimental manufacturing process.
- The results found that robots struggled with delicate tasks such as placing iPhone screws and applying glue.
Apple has reportedly been experimenting with automated iPhone assembly in partnership with Foxconn, tests that have revealed robots struggle with the more delicate aspects of iPhone assembly.
As reported by The Information:
Eight years ago, Apple executives including CEO Tim Cook attended a meeting in China where they watched a video of an experimental manufacturing line for the iPad operated by robots rather than humans. Cook and the other Apple executives watched as iPad parts traveled along conveyor belts and were cut, chemically treated, polished, and partially assembled with the help of robotic arms known as Foxbots, according to a person who attended the meeting.
Despite the political risk (the Chinese government would reportedly ask Foxconn why it wasn't hiring more people), testing of the automated assembly began. Foxconn Chairman Terry Gou expected by 2014, Foxconn would be using 1 million robots in its factories.
However, the team met with several challenges. For instance, the screws Apple uses in its products are so fiddly, that the robots couldn't cope:
Building a robot that can fasten screws is among the hardest challenges in the industry. A robot must pick up the screw at a specific angle and align it with a hole using multiple industrial cameras. Apple uses screws so tiny that robots had no way to measure the force used to drill them in. By contrast, human workers can feel the resistance from their hands and can tell when something is off.
The testing also highlighted that apple's specifications for placing glue in products are often down to the millimeter, and that "well-trained Chinese workers were more adept at applying glue than their robot counterparts."
Apple also reportedly tried to automate the production of the 12-inch MacBook, but early trials saw the conveyor system fall foul of erratic movement, and the robot which installed the keyboard using 88 small screws "kept malfunctioning", requiring humans to come in and clean up afterward. The experiment went so wrong, Apple had to delay the 12-inch MacBook by six months.
Automation has however proven useful for some less taxing work, like the testing of some devices, and of course Apple's famous iPhone recycling robot Daisy.
iMore offers spot-on advice and guidance from our team of experts, with decades of Apple device experience to lean on. Learn more with iMore!
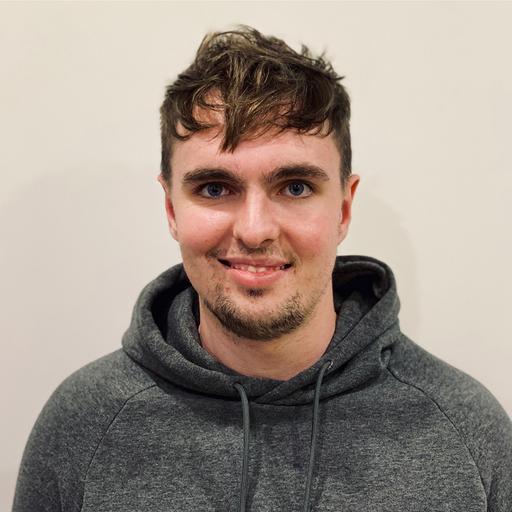
Stephen Warwick has written about Apple for five years at iMore and previously elsewhere. He covers all of iMore's latest breaking news regarding all of Apple's products and services, both hardware and software. Stephen has interviewed industry experts in a range of fields including finance, litigation, security, and more. He also specializes in curating and reviewing audio hardware and has experience beyond journalism in sound engineering, production, and design.
Before becoming a writer Stephen studied Ancient History at University and also worked at Apple for more than two years. Stephen is also a host on the iMore show, a weekly podcast recorded live that discusses the latest in breaking Apple news, as well as featuring fun trivia about all things Apple. Follow him on Twitter @stephenwarwick9